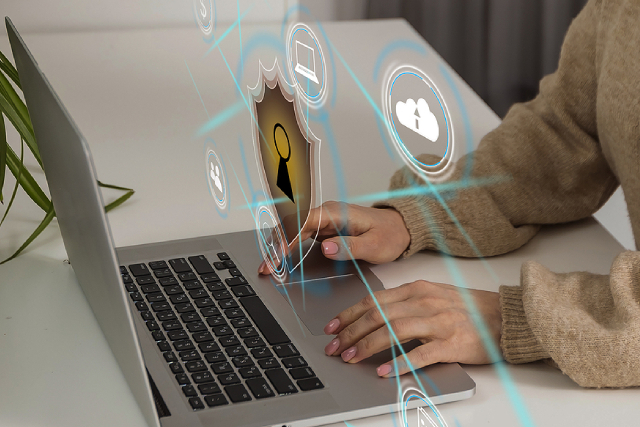
Vital Roles of OT Cybersecurity in Digital Transformation
As industrial sectors ramp up the digitization of their operations to stay ahead of the competition, executives now have a sharpened focus on enterprise-wide cybersecurity. That said, the IT/OT convergence process exposes many critical systems to a high risk of cybercriminals exploiting them.
The SANS 2021 OT/ICS Cybersecurity Survey reveals that 70% of respondents claimed their OT environments were at high or severe risk, a significant increase from 51% in 2019. Meanwhile, 48% were unsure if their organizations had been compromised or not in the past year. Although IT breaches make for better headlines, OT breaches are far more devastating, as successful attacks could potentially lead to physical harm, injury, and death.
With that said, let us get to know the vital roles of OT security in the digital transformation journey of industrial organizations worldwide.
1. Fingerprinting and mapping assets
Organizations undertaking digital transformation focus on three key steps to achieve their goal:
- Identifying and safeguarding critical assets
- Planning and implementing a holistic cybersecurity transformation focusing on IT/OT SOC integration
- Improving operational efficiency and preventative maintenance
We cannot manage what we cannot see, so gaining visibility into the organization’s vital assets and networks is a critical first step. However, this area poses many challenges. For instance, IT teams face great difficulty getting a real-time view of OT assets since they can span a large geographical footprint.
Also, most OT environments are still made up of legacy equipment that may be sensitive to various types of network traffic. This sensitivity often means that even commonly used IT solutions can disrupt these devices and disrupt the safety of plant operations or, at worst, create major outages.
Overcoming these challenges requires an OT security and visibility solution, preferably those built specifically for ICS/OT environments. First, it should primarily provide comprehensive OT asset inventorying and network visualization without risking ongoing industrial processes. Second, the solution must be capable of delivering robust and real-time OT threat monitoring that shortens the mean time between detection and response.
OPSWAT NEURALYZER™ is one solution that fits the bill. It gives full visibility into the organization’s OT assets and networks through continuously discovering and monitoring assets, threats, vulnerabilities, supply chain violations, and non-compliance issues.
2. Integration into the security operations center (SOC)
Industrial systems in the past were rarely considered high risk given that they were not connected to the internet or enterprise systems and only operated in isolation. Since that is no longer the case today, OT integration into SOC is no longer optional due to the ever-increasing cyber risk to OT technology.
There are many benefits to making this integration happen in an enterprise-level SOC, such as:
- The sooner threats are identified (which often originate in IT systems) in the initial stages of the cyber ‘kill chain’, the sooner they can be eliminated.
- Speed up response times by improving communication between OT and IT teams.
- Reduce costs by having one comprehensive SOC instead of multiple and disparate ones.
Organizations can take a page from the U.S. government’s method of addressing these points through their Continuous Diagnostics and Mitigation program. This CDM program proves that it is possible to integrate OT into SOC and roll out enterprise-wide cybersecurity initiatives.
Besides implementing a CDM program, organizations can also implement a number of best practices to better unify their OT and IT, namely:
- Adopt compliance-led initiatives, such as regulatory and compliance alignment, capacity review, and SIEM architecture.
- Implement cyber threat intel capability uplift and other related intel-driven planning methods.
- Conduct assessments through simulation exercises, technical and executive tabletop exercises, and cyber defense readiness.
These initiatives and more like it helps organizations identify their strengths, uncover opportunities for improvement, and create a roadmap to become more resilient and cyber-secure.
3. Enable preventative maintenance
Organizations can leverage the improved asset visibility from step one to identify the root cause of problems in their operations. The rich device data they generate helps eliminate blindspots and allow businesses to quickly get to the root cause of OT issues, whether operational or security-based, and solve them without delay.
Take, for instance, an energy company that adds new equipment to its network and misconfigures them during installation. This error causes network congestion in their OT environment that slowly increases over time, reducing equipment lifespan and output while raising operating costs and the amount and extent of repairs.
Businesses can avoid such issues through preventative maintenance via condition-based monitoring, a maintenance strategy that monitors devices continuously to monitor their condition, like degradation, wear, and other relevant changes. Using sensors to stay on top of remote assets provides key data from which one can derive useful insights on reducing the mean time between failure and repair. One might say this approach does not fully qualify as predictive, yet it is still a big help in identifying issues as they develop and enable operators to perform proactive maintenance.
Predictive maintenance keeps predictable problems from popping up. In OT environments, these issues can cost industrial organizations millions of dollars. Thus, asset visibility and its impact on predictive maintenance are truly game-changing, including reduced costs, vastly improved uptimes, fewer safety risks, and extended equipment lifespan.
Conclusion
The move towards digitalization is sweeping across various industries worldwide, including the industrial and critical infrastructure sectors. But with this trend comes new threats and vulnerabilities that could impact OT technology, many of which were built decades ago and are not designed for secure network connection. As such, it is vital to incorporate OT security into the digital transformation journey and keep it up to date with modern standards.
If you need assistance digitizing your organization’s operations, Allied Solutions can provide you with the total industrial automation solutions you need to succeed. From IT and OT cybersecurity solutions to manufacturing execution systems, we supply a wide range of products that can advance the productivity of your manufacturing operations. To learn more about our OPSWAT solutions or other products, such as GE Proficy Historian, ST Engineering Data Diode, and more, don’t hesitate to contact us today.